With his thoughtful, measured delivery, Jon Partington is clearly very much the engineer. That he is no longer quite the Englishman he was, is no fault of his own. A few years of living in Australia will do that to anyone’s vowels. Jon and I had arranged to talk on the phone a few days earlier, but his demanding schedule got in the way. But today, I have him, and he’s all apologies - still British in that regard. Discussions of tea, the weather and the smallness of the world follow before I ask this one-time race car engineer his own chicken and the egg conundrum - what came first, cars or bikes? “Cars definitely,” he admits. “Although it was a guy I worked with when I first started my automotive career that first introduced me to road bikes, and from then on, I was all in.”

With its brazed together frame and downtube shifters, Jon’s first bike, gifted by the same work colleague who thought the twenty-something Jon could really do with quitting smoking and drinking a little less, kickstarted a journey that saw him pedal into the ranks of the Cat 1 circuit, one step down from pro-pro. In other words, he got fast, fast.
Between bike racing at the weekend, building his own tools and rebuilding his beloved Mini on weeknights, Jon’s work in the Automotive Technology sector at Prodrive in Oxfordshire introduced him to the world of concept cars and technology demonstration projects, high level practical experience that would serve as the perfect grounding for Partington Wheels, still a few years and an entire continent away. A move to the design office formalized Jon’s engineering training, where he began designing engines and transmissions, melding years of hands-on know-how with the sort of esoteric design skills that reached far beyond the world of race cars.
Uniquely, Prodrive also hosted staff sports days, which often featured a very muddy mountain bike race or two. “Engineers are often pretty attracted to mountain biking,” Jon says, who now counts himself as a regular on the rough stuff. “It’s something about the allure of taking things apart and fixing them that makes it all the more instinctual to an engineer - that and the suspension, of course!” By comparison, road bikes can seem precious, prickly even. Who amongst us hasn’t regreased a road bike hub at home and sat back to admire it with a happy sigh, only to have a spare bearing roll merrily to their feet? Don’t forget me!

But back to today, and Jon is in Australia. How did that come about? “Well, the global financial crisis had hit, and come 2010, the U.K. arm of Prodrive was, like many other businesses back then, struggling to stay afloat,” he says. “So I got offered a secondment out to their Australian branch on the outskirts of Melbourne in Victoria. But long story short, my deployment there got canned once I arrived as the U.K. arm wanted me back, so Caroline, my then-girlfriend and now wife, decided to stay and make a go of things anyway.”
A brief stint at Ford in Geelong followed, but the fragmented, over-large corporate culture quickly blunted Jon’s creative ambitions. Feeling somewhat jaded with the automotive industry, and with a growing desire to turn his engineering talents towards the bike, Jon decided to complete his engineering degree, a course that exposed him to the world of carbon fibre and an intriguing final year project with the Defence, Science and Technology organization. Much analysis of imperfect helicopter carbon fibre followed, including voiding, compression in the laminate and tricky questions of compressive fatigue durability. Luckily for the chopper’s crew, Jon quickly devised a wholly new method of accelerated fatigue durability testing that accurately predicted the lifespan of the troubled part. And he still had time for tea and crumpets. “I like the multi-dimensionality of carbon fibre and the fact that as a material, it’s quite young,” he says. “There’s a lot of creative freedom - it’s a new material in that sense.” Unlike, say, steel? “Exactly. Metal has been around for hundreds of years, and there are well-developed processes for working it. And while a lot of innovation still happens, especially in the bike space, I didn’t feel that I could bring anything new to the table.”

Carbon fibre has been used to make plane wings since the 1970s, but in terms of its potential for mechanical strength, Jon realized that there still wasn’t the know-how, design or technology to deploy it effectively in other areas, like bike wheels. And as luck would have it, Deakin University in Geelong had just opened a purpose-built research facility called Carbon Nexus, a collaborative initiative between industry and academia. A carbon candy shop, if you will, complete with a commercial-scale R&D pilot line for producing carbon fibre, the only place in the world where one can develop commercial carbon fibre, from the very filaments to the recipe of process parameters.
If Willy Wonka had a penchant for composites, you’d find him at Carbon Nexus.

Enticed to stay on for a P.H.D. off the back of his final year helicopter project, Jon delved into the world of carbon fibre parts design and deployment, in the process, finding out that the use of carbon fibre is woefully misplaced. “Making a car door, bonnet or roof skin out of carbon fibre is a pretty crap use of the material,” he says. “On the other hand, underneath the car, where you have all of these structurally-loaded parts, is exactly where you should be using the material. But the design and manufacturing practices to make those parts don’t exist, so that’s what my P.H.D. covered - novel design methods and manufacturing processes for the production of complex carbon fibre parts.” And if that's not the name of a Japanese prog-rock band, I don't know what is.
Off the back of Jon’s P.H.D. came interest from futurists looking to tap his expertise, and at the same time, the idea of making a bike wheel, a product he saw as the perfect medium for carbon fibre innovation. “Sadly, my grandma had just passed away, but she left me a small sum of money in her will,” he says. “With that little bit of cash, I felt ready to put my know-how into practice and make my own wheel.” Having sourced pre-materials from the U.K. (Carbon Nexus deals in filament, not fabric-form carbon fibre complete with resin), and some primitive mold tools made in China, Jon successfully put together a first wheel concept, a world away from the final R-Series, but the first iteration of what would become a Partington wheel. Albeit with a hiccup or two along the way. “I had to use vacuum pumps as part of the process,” he begins, “and they put out a lot of smoke. Around that time, of course, the show Breaking Bad was getting quite popular, so I had some explaining to do to my neighbors. Once I showed them what I was doing, relations improved, although I’m not sure if they thought what I was doing was any better than cooking up drugs!”

Pleased with his first wheel (“on reflection, I was woefully naive about how close I was to it being ready for the market”), Jon decided to push on, and for the next five years, he worked hard to develop his designs, before finally securing some government funding that would see him move into a bay at ManuFutures, an advanced manufacturing innovation hub to start producing his first commercially-viable wheels. Small business woes, familiar to anyone brave enough to do their own thing, followed, but so did early recognition courtesy of the Handmade Bike Show in Melbourne and an article by Cycling Tips that revealed Partington to the wider cycling world. “I think they thought we were a bit of noise that would disappear in time, “ Jon says, laughing at the memory. “But we sold a dozen pair of wheels off the back of that - our first to a nice chap from Denmark who still emails with friendly notes to this day - and we were off and rolling.” Which must have felt pretty amazing? “Yes and no,” he admits. "The gravity of what we do is never lost on me. Wheels are a safety critical component, so yes, while we were happy to start selling, as an engineer, even though I know the wheels pass all of our internal tests very comfortably, you are still nervous about your product being used, or abused in the wild. We wouldn’t be doing our job unless we concerned ourselves with that.”
Of course, a conversation about carbon fibre bike components isn’t complete without talking about weight. And that’s a tough proposition for any company, satisfying the market’s desire for lightweight while building a durable product. “It’s a tricky balance of attributes,” Jon says. “But ultimately, you need to differentiate from what’s out there. In my mind, you can buy a largely proven open-mold wheel in China, whack a sticker on it and have a company that is essentially a marketing exercise - plenty of those about. There’s nothing new there, no innovation, but you’ll probably have a lot of pretty pictures. Or, you can take a technical approach, where you make your wheels in-house, as we do, and embrace a certain angle. For us, that’s performance, the last ten tenths.”
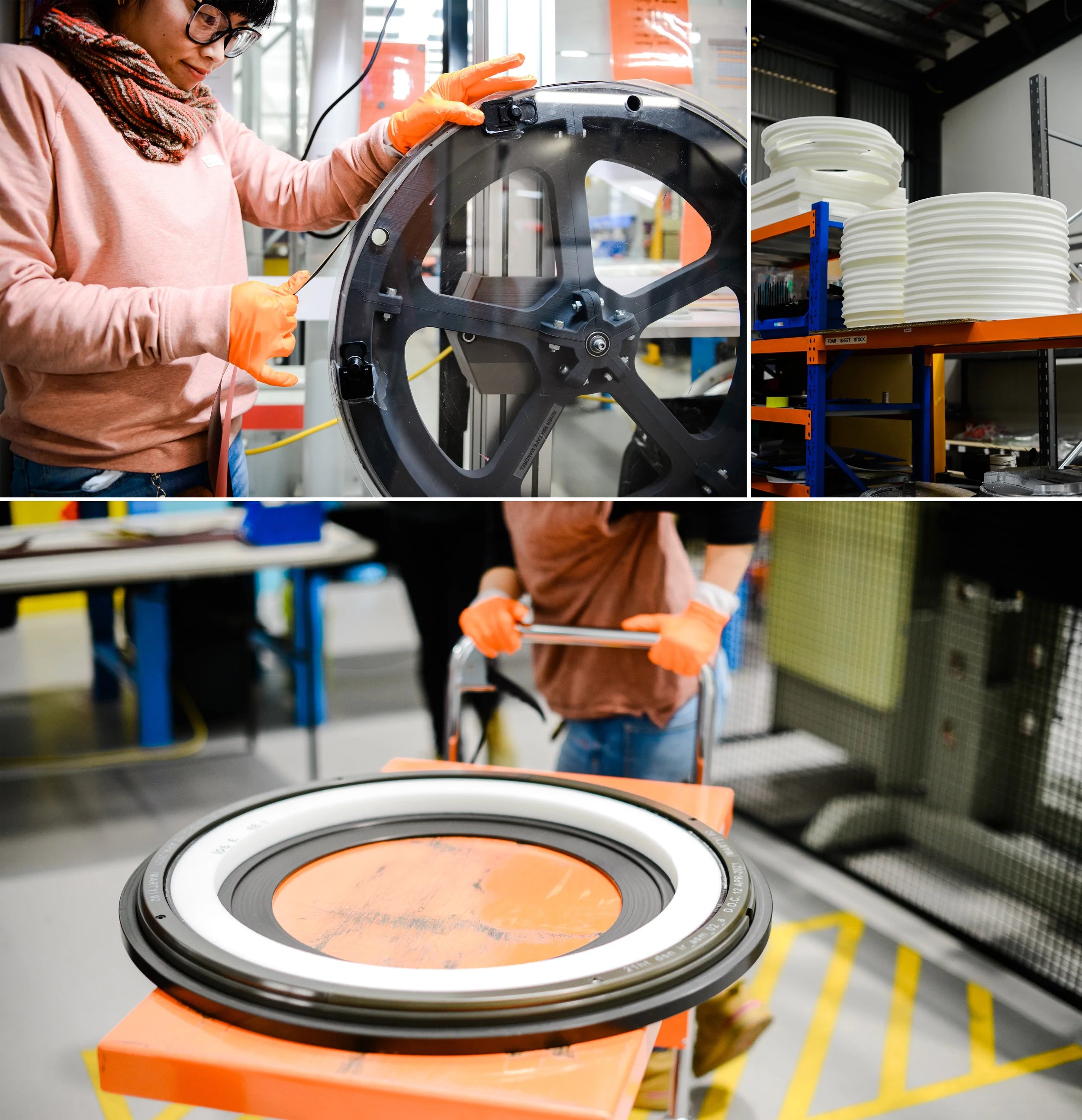
And where does weight factor in? “It’s an engineering problem. To my mind, making everything thinner is not how you make a lighter product. It’s a slow creep to a line you can never cross,” he says. It turns out that the automotive world is not the only sector where companies are using carbon fibre, but few of them well. In Jon’s opinion, the cycling industry was barely scratching the surface of the true potential of the material. “If you properly understand carbon fibre, and set some clear design philosophies on how you are going to use it, and don’t compromise on those, you can ultimately make a very light product that relies on design innovation, not simply thinner materials margins.” The risk, of course, is that high-end bike wheels are seen as Sunday specials, wheels you pull out to look nice, not compete. “That’s exactly what I don’t want Partington to be, “Jon emphasizes. “Carbon fibre itself doesn’t fatigue. That’s not true of the resin of course, but if you can design something so all the load is going into the fibres, not the resin, then you can make a product that is actually very durable and will last a long time.” In other words, Jon wanted everything - light, fast, durable and strong. And does he think he has achieved that? “Well, we were relentless in finding a design solution to meet those demands, “ he says. “That’s what drove the architecture and the aesthetic of the spokes. It’s all the product of a sound design rationale to keep loads in the fibres; some of the components we have in the rim have a similar effect, essentially using all of the materials as sympathetically as possible.”
An honest, high performance wheel you can use every day? Make mine a Partington.

Finding a pair of Partingtons right now is a tricky business. But here at Above Category, we've got an exclusive, limited supply of Partington's R-Series wheels arriving monthly. And with the next shipment set to land with us in mid-September, head over to the Partington product page to pre-order a set and treat yourself to the ultimate riding experience.